At present, there are hundreds of PLC models produced by manufacturers both domestically and internationally, each with unique performance characteristics and varying price ranges. Therefore, when designing a system, it is essential to prioritize the principle of model uniformity. It is recommended to use the same series of PLCs that the company already has in place as much as possible. This approach not only simplifies learning, mastering, and maintenance but also enhances the availability of spare parts and reduces programming costs.
This paper primarily focuses on the structure of elevators, the key technologies involved in elevator control systems, and the design of the electrical control system.
**First, the key technology of the elevator control system**
**1. PLC Control Technology**
PLC, or Programmable Logic Controller, is an advanced industrial control device that integrates microelectronics, computer technology, automatic control, and communication systems. It was developed to replace traditional relays and perform logical operations, timing, counting, and sequence control functions. According to the International Electrotechnical Commission (IEC), a PLC is a digital electronic system designed for industrial applications. It uses programmable memory to store instructions for performing logic operations, sequence control, timing, counting, and arithmetic functions. These instructions are used to control various mechanical or production processes through digital and analog inputs and outputs. The design of the PLC and its related equipment should allow for easy integration into industrial control systems and support future expansion.
**2. Communication Technology Based on RS-485**
The RS-485 bus interface is a widely used serial communication standard known for its ease of network connection, strong anti-interference capability, and long transmission distance. It utilizes balanced transmission and differential reception, which allows it to effectively reject common-mode interference. With high sensitivity, it can detect voltages as low as 200mV. The reliable communication distance can reach several kilometers. Using RS-485, multiple systems can be interconnected using just one pair of twisted wires, making it cost-effective, simple to implement, and ideal for long-distance communication.
**3. Configuration Technology**
With the rise of distributed control systems, the concept of "configuration" has become increasingly familiar to automation engineers. As PC technology continues to advance, it has proven to be more advantageous than previous dedicated systems. PCs offer faster development, mature supporting technologies, lower total cost of ownership, abundant software and hardware resources, and strong interoperability. Additionally, PC-based control systems are user-friendly and supported by a wide range of technical resources. In this context, configuration software plays a crucial role. It serves as a platform for data acquisition and process control, enabling users to quickly build monitoring functions for industrial automation systems. Configuration software supports a variety of industrial devices and communication protocols, and often includes distributed data management and networking capabilities. Before the emergence of configuration tools, building HMI applications required manual coding or third-party development, which was time-consuming, inefficient, and unreliable. Alternatively, users had to purchase closed systems, limiting their ability to interact with external systems and upgrade features. Configuration software solves these issues by allowing users to create custom application systems tailored to their needs. As technology evolves, configuration software continues to expand, incorporating real-time databases, real-time control, SCADA, communication, open data interfaces, and extensive I/O support.
**Second, the Components of the Elevator System**
The elevator system consists of two main parts: the physical structure and the controller. The physical structure includes the base, column, car, and internal and external call panels. The controller comprises the PLC, frequency converter, and power supply. The elevator is divided into eight floors, each equipped with a floor number display, an external call button, and a registration mechanism. The internal call panel contains buttons for selecting floors, door opening/closing controls, and indicators for call registration and elevator movement direction.
**Third, the Design of the Elevator Electrical Control System**
The internal call panel includes eight floor selection buttons, door operation switches, and displays for call registration and elevator movement. Each floor’s external call panel has up and down buttons and indicator lights. The floor number display circuit uses the CD4511 IC for seven-segment decoding, reducing the number of PLC output points compared to direct decoding. All floor displays, external call buttons, and registration indicators are mounted on long narrow circuit boards, with two boards installed across all eight floors.
The PLC selected is the Mitsubishi FX2N-80MR, while the frequency converter is the FR-S520S-0.4K-CH(R). A switching power supply provides 5V/5A and 24V/1A outputs. The 5V supply powers the external and internal call circuits and small signal processing components, while the 24V supply powers the door motor and voice station amplifier circuit. The main control board has a power socket and safety socket with a 250V/10A fuse. The elevator operates on AC 220V at 50Hz, using a three-core single-phase socket with protective grounding.
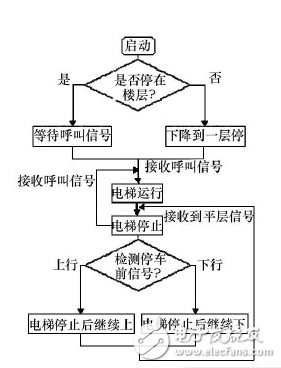
**1. Elevator Input Signals and Their Significance**
(1) Position Signal: Generated by eight sensors (XK1–XK8) located at each floor, these signals activate when the elevator reaches a specific floor.
(2) Command Signal (Internal Call): Eight command signals from buttons labeled K11–K18 indicate the desired floor for passengers inside the elevator.
(3) Call Signal: Fourteen call signals from buttons K21–K34 represent external requests. For example, pressing K23 indicates a request to go up from the second floor.
(4) Door Control Signals: Two signals for opening and closing doors, along with two signals indicating door position.
(5) Photoelectric Encoder Pulse Signal: Used for precise positioning and speed control.
**2. Elevator Output Signals and Their Significance**
(1) Running Direction Signal: Two arrow indicators show the elevator’s direction of movement.
(2) Command Registration Signal (Internal Call): Eight indicators (L11–L18) confirm that an internal call has been registered.
(3) Call Registration Signal: Fourteen indicators (L21–L34) show that an external call has been accepted.
(4) Floor Digital Display Signal: BCD code is decoded using CD4511 and displayed on a seven-segment LED.
(5) Door Action Signals: Two signals for door operation and four signals for elevator movement, including high and medium speed control.
(6) Voice Station Control Signal: Manages the voice announcement system.
(7) Alarm Ringing Output Signal: Triggers an alarm if needed.
**3. PLC Input/Output Port Assignment and External Wiring**
All input and output signals in the elevator system are assigned to the corresponding PLC ports. X0 is connected to the pulse signal from the rotary encoder. The inverter is controlled via I/O mode, and all power, signal lines, and wiring are properly connected. A power-on check is performed to ensure everything is functioning correctly. Input signals are tested by pressing leveling switches and call buttons to verify indicator lights. Output signals are checked by running a simple test program to confirm that all connected devices operate as expected. To prevent overtravel, limit switches are installed above the eighth floor and below the first floor. If the elevator exceeds its normal range due to a program error, the limit switch will stop the inverter, ensuring the elevator does not exceed the designated floors.
5V Ac Dc Adapter,Power Adapter 5V,Dc 5V Adapter,5V Ac Adapter
ShenZhen Yinghuiyuan Electronics Co.,Ltd , https://www.yhypoweradapter.com