1 Comparative analysis
At present, most of the anti-collision devices of electric locomotives rely on the elastic bumper to passively buffer and absorb part of the collision energy to reduce the impact of the impact. However, when the locomotive collides, its anti-collision effect is negligible. The underground environment of the coal mine is special, the tunnel is narrow, there are many bends in the turnout, and the maximum distance between the tunnel wall and the rail is less than 1 In. When the electric locomotive travels to bends and turn lanes, the electromagnetic waves or light emitted by the transmitter installed on the electric locomotive itself is easily reflected by the wall of the roadway or passing vehicles in the roadway, causing the brake device to falsely alarm and malfunction. Secondly, the braking device is braked by mechanical mechanisms such as hand brakes, motor levers, etc. The reaction speed is slow or rapid, and the braking is not stable. It is also easy to cause the vehicle to fall off the road or damage the equipment, and even cause personal injury. Therefore, this type of braking device is not suitable for use in coal mines, and may also leave hidden safety hazards.
Based on years of experience, theoretical knowledge and accident cases, combined with the characteristics of various vehicle anti-collision devices currently on the market, a downhole intelligent electric locomotive anti-collision system solution was designed.
2 System characteristics
1) Underground intelligent electric locomotive anti-collision system uses infrared as a distance detection light source, which has strong anti-interference ability and high reliability, and is not interfered by electric locomotive headlights, roadway lighting, workers' miner's lamps and other electromagnetic waves. The infrared transmitter and receiver are installed separately, and will not malfunction due to the signal reflected by the vehicle or the roadway wall.
2) The system uses a single-chip computer as the main controller and uses its super data calculation and information processing capabilities to truly achieve the purpose of intelligence and automation, greatly improving the reliability, stability and intelligence of the system. Make the operation of the electric locomotive safer.
3) When the electric locomotive enters the different range of infrared rays in front, the system can automatically rely on the microcomputer single-chip microcomputer to calculate the current running speed and relative distance of the electric locomotive to send out an audible and visual alarm signal. Throttling enables soft braking before the danger of a collision. The braking is fast and smooth, ensuring the safety of personnel and vehicle equipment, and avoiding unnecessary losses of personnel and equipment due to severe collisions and excessive braking.
4) If additional LED or LCD display devices are added, the system will be more intuitive and complete, and the functions will be more powerful.
3 System composition
The intelligent anti-collision system of electric locomotive is mainly composed of infrared transmitting unit, infrared receiving unit, main control unit, execution unit, sound and light alarm unit and hydraulic brake unit.
The infrared transmitting unit includes a code modulator, carrier oscillator, electronic switch, transmitting tube, condenser lens, etc .; the infrared receiving unit is an infrared integrated integrated receiving head; the main control unit is composed of a microcontroller, a clock circuit, a reset circuit, and a manual operation keyboard 〠D / A converter; the execution unit is composed of photoelectric isolator and analog amplifier; the sound and light alarm unit is composed of electric car whistle and flash alarm circuit; the hydraulic brake unit is composed of speed sensor, hydraulic oil pump, proportional solenoid valve, overflow Flow valve, hydraulic cylinder, brake push rod, etc.
4 System requirements
1) "Coal Mine Safety Regulations" stipulates: "When two locomotives or two trains are traveling in the same direction on the same track, they must maintain a distance of not less than 100m. The braking distance of the train when transporting personnel must not exceed 20m. Secondly, the curve radius of the underground roadway is generally around 25Ill. Therefore, the system calculates and sets system parameters according to the most dangerous driving on the same track. In the infrared emission unit, the emission distances of the three infrared emission tubes are respectively adjusted to an alarm distance of 80m, a general braking distance of 50m, and an emergency braking distance of 7m.
2) Considering the humid environment in the coal mine, especially in the summer, the track surface adhesion coefficient is lower and it is easy to slip, so the braking distance of the motor train is set to three kinds of alarm, 20m, 2m, so that there is still a certain amount of left after the train brake Buffer distance to prevent skidding from affecting the braking effect of the locomotive. According to the trigonometric formula α = 2arctan (a / b) (where a is the maximum beam radius and b is the beam range, ie the maximum emission distance), the infrared tube emission angles are calculated as 44 ', 68' and 8 °, that is, each emission tube When the maximum range is 80m, 50m, and 7m, the maximum beam diameter is 1m (the width of the electric locomotive). The beam covers the end face of the electric locomotive without affecting other vehicles, ensuring sensitivity and reliability.
3) According to the characteristic that the single-chip microcomputer can only process one signal at a time, the duty ratio of the high-frequency modulation pulse of each transmitting tube must be controlled below 1/3 to make it work in turn, which reduces the working current Reduced power consumption without causing signals to interfere with each other, causing misdetection and improving system reliability.
4) According to the regulations of “Maximum speed limit of straight road 5m / s and curve 2m / s in the“ Coal Mine Safety Regulations â€, it is required when the program parameters are set: When the electric locomotive enters the set braking distance, the single-chip computer according to formula = V2 / 2L Calculate the brake acceleration (where V is the current vehicle speed, the maximum braking distance), that is, the single-chip microcomputer automatically controls the brake acceleration between 0.6 ~ 4m / s2, and issues a braking command, adjusts the proportional solenoid valve to control the brake The pressure makes the train brake and stop smoothly within the prescribed displacement.
5 Working principle
The principle of the intelligent electric locomotive anti-collision system, see Figure 1.
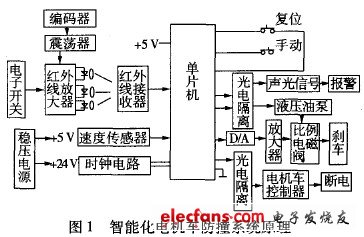
1) Three different coded signals of the code modulator of the infrared emitting unit modulate the carrier signal of 38 kHz, generating three different frequency modulation signals to the amplifier to drive three infrared emitting tubes, emitting three different coded infrared. According to the characteristic that the single-chip microcomputer can only process one signal at a time, the three-way amplifier is controlled by the electronic switch to turn on in turn, ensuring that only one transmission tube works at a time, which reduces the working current, reduces power consumption, and avoids The signals interfere with each other, causing the receiver to misdetect.
Through the selection of the launch tube and the adjustment of the amplifier's transmit power, the launch distance is S1 = 80m, S2 = 50m, S3 = 7m; by adjusting the focal length of the respective lens group, the beam angle is α1 = 44 only α2 = 68 ', Only α3 = 8 °, the beam diameter at the critical position of each launch distance is 1m, which just covers the end face of the motor train, which not only ensures the reception but also prevents interference to vehicles in adjacent lanes. The launching unit is installed at a proper position under the lighting headlight of the electric locomotive and under the tail light of the train. Since the underground rail transport electric locomotive and the train travel in both directions, the infrared emitters are installed at both ends of the locomotive and the train (mining car). The infrared receiving head is installed at a position where the motor head and the transmitting unit are directly opposite.
What can the Screen Protector Cutting Machine do?
This is a customized universal cutting machine that can cut Screen Protectors and Back Filmns suitable for mobile phones,
iPads, smart watches, macbook etc.
One Cutting Machine can cut all types of Mobile Phone Screen Protectors. The cutting accuracy is 0.1mm. It can cut more
than 22000+ mobile phone models and styles, and any model can be cut. 0 inventory, no need to worry about large
inventory, to meet the large needs of customers.
In the Mobile Phone Screen Protector industry, in order to meet the requirements of consumers in the traditional mobile phone film business model, many practitioners will prepare a large number of Mobile Phone Screen Protectors for popular mobile phones. However, the alternate iteration of new and old mobile phone models is too fast, and the cycle is greatly shortened, resulting in many screen protectors that have not been able to be sold in time, and can only be disposed of by themselves. and profit margins will suffer as a result. It is against this background that the Screen Protector Cutting Machine was born, and its appearance can improve the operating status of the Screen Protector industry.
Protective Film Cutting Machine,Back Sticker Cutting Machine,Phone Sticker Cutting Machine,Flim Cutting Machine
Shenzhen TUOLI Electronic Technology Co., Ltd. , https://www.szhydrogelprotector.com