Many industries require electronic equipment that can operate reliably in harsh environments such as extreme heat. Traditionally, engineers must use active or passive cooling techniques when designing electronic equipment that needs to operate outside of the normal temperature range, but some applications may not be able to cool, or electronic equipment may be more advantageous when operating at high temperatures. Improve system reliability or reduce costs.
The oldest and currently the largest high-temperature electronics (>150°C) application area is the underground oil and gas industry (Figure 1). In this application, the operating temperature is a function of the depth of the subterranean well. Global geothermal gradients are typically 25 ° C / km depth, and some areas are larger.
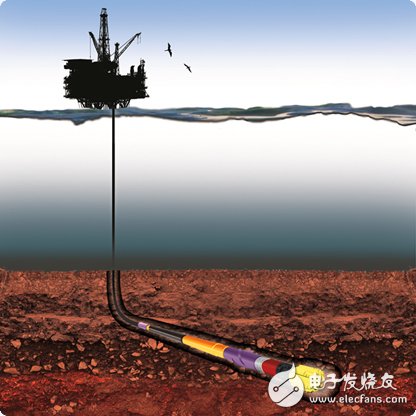
Figure 1. Underground drilling operations
In the past, drilling operations were carried out at temperatures ranging from 150 ° C to 175 ° C. However, due to the reduction of underground natural resources and the advancement of technology, the drilling depth of the industry began to deepen and the geothermal gradient began to increase. Drilling in the area. These harsh underground wells have temperatures in excess of 200 ° C and pressures in excess of 25 kpsi. Active cooling technology is less realistic in such harsh environments, and passive cooling technology is less effective when heat is not limited to electronic devices.
The application of high temperature electronic equipment in the underground drilling industry is very complicated -
First, during drilling operations, the electronics and sensors guide the drilling equipment and monitor its status. With the advent of directional drilling technology, high-temperature geosteering instruments must accurately guide the location of the borehole to geological targets.
Second, the precise downhole instrument collects the surrounding geological structure data at the time of drilling or just after the drilling. This practice is called logging to measure resistivity, radioactivity, sound propagation time, magnetic resonance, and other properties to determine geological structural characteristics such as lithology, porosity, permeability, and water/hydrocarbon saturation. Through these data, geologists can determine the type of rock from the structure, determine the type of fluid present and its location, and whether the fluid-containing region can extract a sufficient amount of hydrocarbons.
Third, during the completion and production phases, the electronic system monitors pressure, temperature, vibration, and multi-phase flow, and actively controls the valve. To meet these needs, a complete high-performance component signal chain is required (Figure 2). System reliability is the most important factor because equipment failures can result in extremely high downtime costs. It takes more than a day to overhaul and replace a drill string that runs underground for miles, and it takes about $1 million a day to operate a complex deepwater offshore rig!
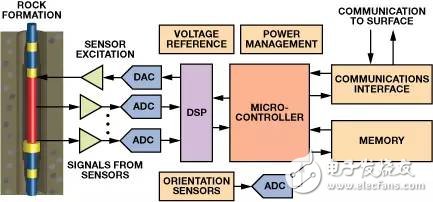
Figure 2. Simplified logging instrument signal chain
In addition to the oil and gas industry, the demand for high temperature electronic devices is increasing in other applications such as avionics. Today, the aviation industry is increasingly moving toward the trend of "multi-electronic aircraft" (MEA). This solution is on the one hand to replace the traditional centralized engine controller with a distributed control system.
Centralized control requires a large, heavy-duty wiring harness consisting of hundreds of conductors and multiple connector interfaces. The distributed control scheme places the engine control system closer to the engine (Figure 3), reducing the complexity of the interconnect by a factor of 10, reducing the weight of the aircraft by hundreds of pounds and increasing system reliability ( The estimate is somewhat related to the number of connector pins (calculated according to MIL-HDBK-217F).
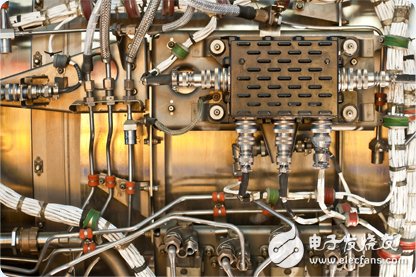
Figure 3. Control system installed on the aircraft engine
However, the price is that the ambient temperature near the engine will rise (–55°C to +200°C). Although the electronic equipment in this application can be cooled, it still has an adverse effect for two reasons.
1) Cooling will increase the cost and weight of the aircraft;
2) Failure of the cooling system can cause the failure of the electronic equipment that controls the critical system (and the most important point) .
Another aspect of the MEA solution is the replacement of hydraulic systems with power electronics and electronic controls to increase reliability and reduce maintenance costs. Ideally, the control electronics must be close to the actuator, which also produces a higher ambient temperature.
The automotive industry offers another emerging application that uses high-temperature electronics. Like avionics, the automotive industry is shifting from purely mechanical and hydraulic systems to mechatronic systems. This requires positioning sensors, signal conditioning, and control electronics that are closer to the heat source.
The maximum temperature and exposure time depend on the type of vehicle and the location of the electronics in the vehicle (Figure 4). For example, highly integrated electrical and mechanical systems, such as gearbox configurations and gearbox controllers, simplify the production, testing, and maintenance of automotive subsystems. Electric vehicles and hybrid electric vehicles require high-energy-density electronic devices that are used in converters, motor control, and charging circuits.

Figure 4. Typical car maximum temperature range 5
E-cig as a substitute of tobacco mainly reminds people of its potential benefits for health. Four ingredients contain in the e-liquid : propylene glycol, glycerin vegetable, nicotine and food grade essence. Nevertheless, smoke from cigarette contains carbon monoxide, tar, arsenic, ammonia, and many other cyanide and acetone.
Advantage
- New ceramic self heating element, Uniform heating
- High reduction, Temperaturecan be accurately controlled
- Safety and Health, Worth a product,Natural and realistic taste,Factory Direct Sale
- Using proprietary technology,Quality assurance, trustworthy
- Oil leakage free, compact, pocket-sized, portable and easy to transport
-
So that smokers can smoke addiction, refreshing, to meet the psychological and physiological needs of smokers, and in line with the habit of smokers for many years.
-
Compared with rechargeable e-cigarettes and mechanical e-cigarettes, the price of disposable e-cigarettes is much lower, which is applicable to a wider range of customers than the first two. It is also the absolute truth for ordinary consumer groups to be cheap.
Wax Device Oem,Thc Wax Device Oem,Marijuana Wax Device Oem,High Cost Performance Wax Device
Shenzhen MASON VAP Technology Co., Ltd. , https://www.disposablevapepenfactory.com