Programmable logic controllers (PLCs) and temperature controllers have similar benefits in manufacturing, ensuring effective process control, achieving consistent quality, and minimizing user error.
Process control equipment has been presented in various forms since the 17th century, such as temperature regulators in furnaces and later in the 18th and 19th century steam engines, boiler valves, and other ball governors in mechanical systems.
PLC is a more modern tool that emerged in the 20th century (especially in the 1970s) with increasing demand for factory automation. Prior to PLC, its function was achieved by a series of mechanical components that were extremely expensive to install and maintain, and were very complex and difficult to change when the plant needed adjustments (such as product line upgrades).
However, despite the many similarities between temperature controllers and PLCs, there are still significant differences in setup, programming, and application, and combining these differences, temperature controllers have their own unique advantages:
Cost savingsOf course, this is relatively speaking. The PLC is designed to control multitasking and is suitable for applications with multi-temperature loop control. For some single loops, or a few loop control applications, many of the features of the PLC are not required for the application, so the cost is high, it is better to choose a controller specifically designed for temperature regulation.
2. Simple setupAs mentioned earlier, PLCs are designed for multitasking environments, so professional programming skills and a lot of time are required to create a solution that meets the needs of a particular application. Temperature controllers can be installed, set up, and optimized relatively quickly (such as PID controllers) with minimal experience.
Many temperature controllers can be panel mounted, that is, they can be mounted on the front panel of the process machine with a visual screen that allows the person to complete the setup in minutes with basic engineering knowledge. PLCs are more complex, usually installed in the rack behind the panel, without a display, and require a separate HMI (also need to be set), so the convenience of setting is obvious.
Temperature controllers are specifically designed to handle specific industrial processes and therefore include features, outputs, and control functions directly related to these processes, such as specialized algorithms for applications that require valve motor drive control (VMD). PLCs need to be characterized by a wide range of manufacturing and automation functions, so the characteristics for temperature control are limited. They can perform basic temperature control tasks, but not as obvious as the special temperature controller. In addition, due to the need to process analog signals, temperature control systems are very demanding on microprocessors. The temperature controller is designed to handle these needs, and the PLC must be tested before the system can determine whether these process requirements can be met. If the requirements are not met, the PLC will not be able to respond quickly to changes in the process and lead to lead or lag, which will affect the quality of the product.
4. Clear visual interfacePanel-mounted temperature controllers come in a variety of sizes and levels of complexity, so operators can easily view process information and warning or alert information that requires attention. PLCs usually do not have a direct interface, but instead require a separate HMI and the HMI needs to be set up separately. HIMI can display the necessary process information, but it also typically displays various data related to other tasks managed by the PLC. This means that the panel-mounted temperature controller has an obvious advantage, with a dedicated interface for easy viewing of all relevant information and quick adjustments. Many temperature controllers also provide additional data logging capabilities that can be used to view previously made changes and flag potential problems.
The temperature controller is part of a closed feedback loop that actively tracks the deviation of the process value from the setpoint and adjusts the power level as needed. Many controllers have a PID algorithm with automatic adjustment that allows for quick setup and keeps the minimum process value from the setpoint deviation. This includes adjustments for unexpected process changes or interruptions (such as oven door opening). This is necessary to maintain a consistently high product quality and to reduce bad product batches.
PLCs sometimes have a PID function, but unlike temperature controllers, their PID functions are usually limited or require manual adjustment by engineers, which makes programming time longer and poses a risk of human error. As mentioned earlier, the temperature control processor requirements can be very high. The simultaneous processing of many other tasks by the PLC may result in a slower response to process changes, and thus the accuracy will be lower than that achieved by a dedicated temperature controller.
Temperature control has several advantages over PLC in process control applications. They are quicker to install and set up, operate faster and simpler, offer special temperature control features, and are designed for temperature control to meet the high demands of process control.
If the system requires a higher level of automation that cannot be achieved by the temperature controller, the PLC is a more reasonable solution, however, it is still recommended to use a dedicated temperature controller to compensate for the PLC's lack of temperature control. This can not only utilize the special temperature control features, but also reduce the requirements on the PLC, and there is no problem of slow response and large deviation from the set value, thus ensuring high final product quality.
Door Lock Motor Characteristics 1. No direction: don't need to distinguish the door direction, left and right sides, both inside and outside the door, can be universal. (convenient purchase locks and reduce inventory).
2. Power: the power consumption is only equivalent to one 5 of the electric control lock, electric lock, 3 A magnetic lock power to open the door, often consumes 0.27 A. And spiritual lock unlock instantaneous current is less than 0.5 A, reduced the entrance guard, talkback host power consumption.
3. No collision: close the door without collision, reduces the choice of door closers requirements (not necessarily with 65 kg of door closers, door closers are free to choose to suit the door), to solve the building door because the door closers clash of the hydrodynamic force is too high, it is not easy to make the door more deformation, prolong the service life of the body.
4. The voice is light: close the door automatically locked, no noise, solves the noise due to electric control lock itself.
5. Life is long, life is up to 350000 times
Operating temperature range:
Mini Door Lock Motor should be used at a temperature of -10~60℃.
The figures stated in the catalog specifications are based on use at ordinary room temperature catalog specifications re based on use at ordinary room temperature (approximately20~25℃.
If a lock motor is used outside the prescribed temperature range,the grease on the gearhead area will become unable to function normally and the motor will become unable to start.Depending on the temperature conditions ,it may be possible to deal with them by changing the grease of the motor's parts.Please feel free to consult with us about this.
Storage temperature range:
lock motor should be stored ta a temperature of -15~65℃.
In case of storage outside this range,the grease on the gearhead area will become unable to function normally and the motor will become unable to start.
Service life:
The longevity of Door Lock Motor is greatly affected by the load conditions , the mode of operation,the environment of use ,etc.Therefore,it is necessary to check the conditions under which the product will actually be used .The following conditions will have a negative effect on longevity.Please consult with us should any of them apply.
â—Use with a load that exceeds the rated torque
â—Frequent starting
â—Momentary reversals of turning direction
â—Impact loads
â—Long-term continuous operation
â—Forced turning using the output shaft
â—Use in which the permitted overhang load or the permitted thrust load is exceeded
â—A pulse drive ,e.g.,a short break,counter electromotive force,PWM control
â—Use of a voltage that is nonstandard as regards the rated voltage
â—Use outside the prescribed temperature or relative-humidity range,or in a special environment.
â—Please consult with us about these or any other conditions of use that may apply,so that we can be sure that you select the most appropriate model.
when it come to volume production,we're a major player as well .each month,we rurn out 600000 units,all of which are compliant with the rohs directive.Have any questions or special needed, please contact us, we have the engineer group and best sales department to service to you
Looking forward to your inquiry. Welcome to our factory.
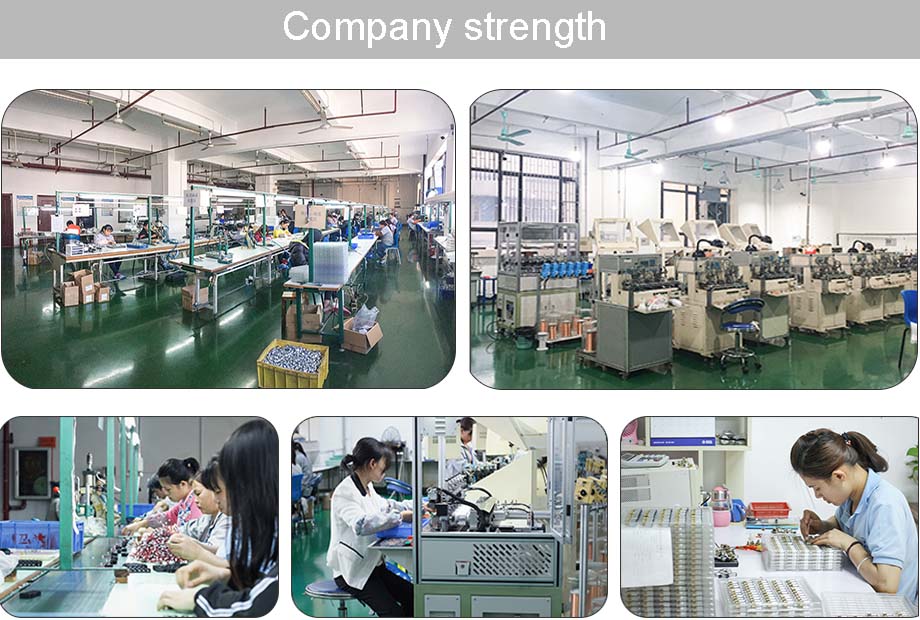
Door Lock Motor,Mini Door Lock Motor,Door Lock Dc Motor,Door Lock Gear Motor
Shenzhen Shunchang Motor Co., LTD. , https://www.scgearmotor.com